Evolving Designs of Advanced Heat Exchangers
Metal Additive Heat Exchanger Roughness
Additive manufacturing enables complex and novel designs which are otherwise infeasible with traditional metal manufacturing techniques. The ability to produce novel designs is particularly interesting in designing heat exchangers where performance is often largely based on the achievable geometry. When compared to traditional manufacturing techniques, heat exchangers made by additive can benefit from the increased surface roughness; however, this effect is not well understood. The design for novel heat exchangers using additive manufacturing must account for the roughness to fully optimize the design. Some baseline and novel heat exchanger designs have been tested for pressure loss and heat transfer performance.

Full size aluminum additive oil coolers with internal enhancement features
Metal Additive Single Channel Heat Exchanger
In addition to creating complex parts using additive manufacturing, the process is ideal for prototyping and testing custom surfaces for heat exchangers. Computational fluid dynamics (CFD) parameter studies are used to find higher performing heat exchanger surfaces to be manufactured via additive manufacturing. These single airside rows are then tested for performance and compared back to the CFD. Roughness from the additive manufacturing process can causes discrepancies between the predicted and actual performance. New engineering correlations are then created to aid with additive heat exchanger design.
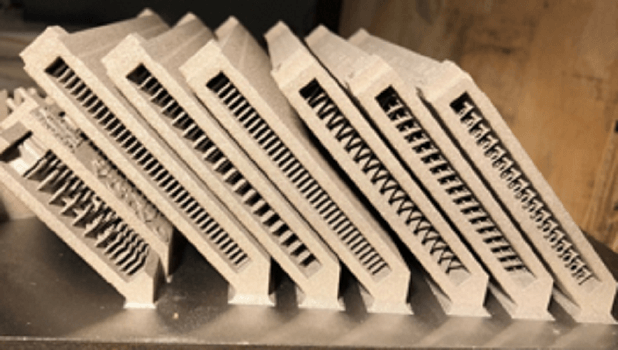
Single heat exchanger fin rows with unique fin designs created with additive manufacturing; stainless steel
Fin Design with Genetic Algorithms
We are using genetic algorithm-based topology optimization combined with Computational Fluid Dynamics (CFD) as a new design tool to produce optimum fin shapes for heat exchangers used in aerospace applications. A rectangular shaped baseline fin geometry is created using voxel representation. An initial population is generated by mutating the baseline fin. OpenFOAM is then used to evaluate the CFD performance of each design, after which the optimization algorithm is applied. The GA sorts the designs using a composite fitness function based on the overall heat transfer and pressure drop, and generates new generations based on mutation and carryover of top performing designs. The percent improvement in the optimum relative to the baseline design can be up to 60%.

Top: The baseline geometry
middle: the resulting optimum fins
Bottom: Fitness Vs. generation.